WHAT ACCENTURE DID Given our long-standing relationship with Rolls-Royce and close collaboration with companies involved with UK Made Smarter, Accenture was asked to provide assistance to the consortium. The aim was to support, over aggressive We manage the order placement, expediting timescales, the scaling up of a new supply chain the payment process and working with DHL and facilitate the rapid assembly of the Smiths who are providing transport and warehousing Group ventilators. services. Parts are inspected and sent onwards to be assembled into ventilators by companies Overseeing the flow of materials, including Rolls-Royce and GKN Aerospace Accenture is integrated with before finally being dispatched for use by the Rolls-Royce sourcing teams to order Department of Health. and stock the right amount of product Working with Avanade, our joint venture with at the various assembly locations. Microsoft, we deployed and now support an Enterprise Resource Planning system (ERP), Rolls-Royce identified more than 100 suppliers Dynamics365, to tightly integrate the supply who could fulfil the engineering design operations and purchasing functions, and have requirement and provide the 292 unique parts. implemented a Procure-to-Pay accounts cycle. Accenture’s role is to precisely coordinate some This automation brings greater efficiency, and 3.4million total parts from the source of supply with the supply chain control tower, enabled to final assembly build. by PowerBI and E2Open software, Accenture provides coordination, oversight and governance across the whole process from start to finish.
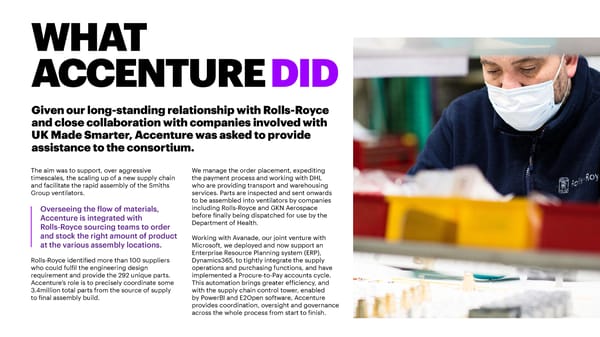